
Development of a LiDAR-based Observation Method for Debris Flows
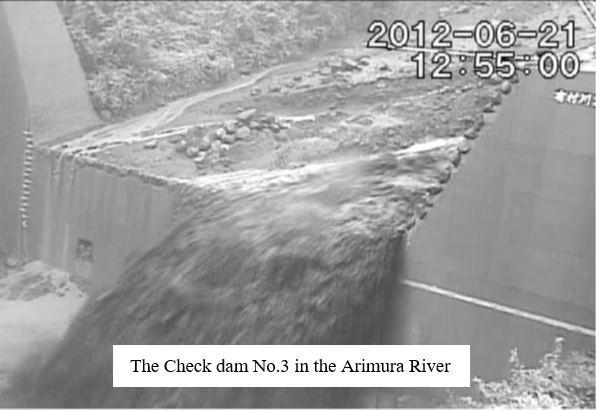
Photo1. Debris flow downstream from
the check dam No.3 in the Arimura River
(Osaka et al., 2013)
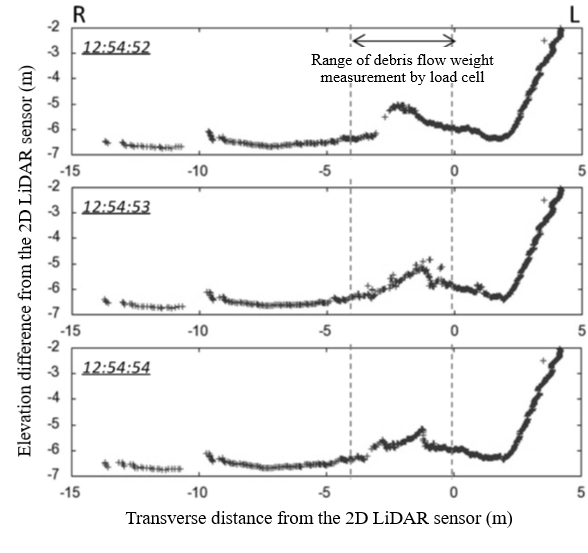
Figure 1. Measurement results by
a 2D LiDAR sensor of the cross-section
of the debris flow shown in Photo 1
(Osaka et al., 2013)
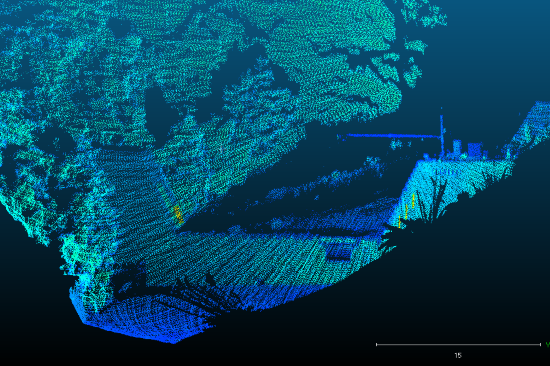
Figure 2. Example of measurement
results by 3D LiDAR sensor
Observing accurate debris flow rates is important for predicting and addressing inundation damage. For this reason, the Volcano and Debris Flow Research Team is developing an observation method for debris flows using LiDAR sensors. LiDAR, which stands for Light Detection And Ranging, is a technology that measures the distance to an object by emitting a laser beam and measuring the time it takes to detect the reflected light coming back from the object. LiDAR sensors have the advantage of being able to measure large areas, with high frequency, day and night. Our team is considering ways to use LiDAR sensors with these strengths for observing debris flows. Therefore, we installed a LiDAR sensor at the spillway of the check dam No.3 in the Arimura River on Sakurajima (Kagoshima City, Kagoshima Prefecture) in June 2012 to observe debris flows that occur several times a year.
Our team first used a two-dimensional ranging LiDAR sensor (hereafter referred to as a “2D LiDAR sensor”) to measure the cross-sectional area of a debris flow. Photo 1 is a cutout of a frame from video footage of a debris flow that occurred on June 21 of the same year. The debris flow can be seen flowing over the spillway of the dam mentioned above, deflecting to the right side of the photo. The unbalanced flow is due to the curvature of the channel upstream of the dam. Figure 1 shows the results of the debris flow measured by the 2D LiDAR sensor simultaneously. In this figure, we can see how the debris flow is biased toward the right side of the figure. These results indicate that, unlike water-level gauges, measuring one point per time step, 2D LiDAR sensors can more accurately measure the cross-sectional area of a debris flow, even in the presence of drift currents.
Next, we used the same 2D LiDAR sensor to measure the velocity of the debris flow. In May 2014, we installed another 2D LiDAR sensor in front of the same dam to measure the falling debris flow as it rushes out of the spillway. The velocity of the debris flow was estimated by fitting measurements from two 2D LiDAR sensors placed in front of and directly above the spillway to an experimental formula (Yoshinaga et al., 2017). This estimation was in general agreement with the result by an ultrasonic velocimetry meter. This result shows that the velocity of a debris flow can be estimated by using only a 2D LiDAR sensor that measures the debris flow surface.
Currently, our team is working on the development of an observation method for debris flows using a three-dimensional ranging LiDAR sensor (hereafter referred to as a “3D LiDAR sensor”). Figure 2 shows an example of measurement results from a 3D LiDAR sensor. The new types of data obtained through debris flow observation by 3D LiDAR sensors may lead to further elucidation of the flow mechanisms of debris flows.
References
1) Tsuyoshi OSAKA, Eiichi TAKAHASHI, Masaru KUNITOMO, Takao YAMAKOSHI, Yukinori NOWA, Hiroshi KISA, Tadanori ISHIZUKA, Rei UTSUNOMIYA, Koji YOKOYAMA, Takahisa MIZUYAMA. Field observations of unit weight of flowing debris flows by force plate in Sakurajima, Japan . Journal of the Japan Society of Erosion Control Engineering. 2013, Vol. 65, No. 6, p. 46-50.
2) Shiki YOSHINAGA, Takeshi SHIMIZU, Tasuku MIZUTANI, Yuya TAKAHASHI, Naoki FUJIMURA, Hiroaki IZUMIYAMA, Tadanori ISHIZUKA. A method for measuring nappe distance and depth of debris flow using laser range finder and application to estimate debris flow velocity . Journal of the Japan Society of Erosion Control Engineering. 2017, Vol. 70, No.1, p. 46-53.
(Contact : Volcano and Debris Flow Research Team)
Examination of the Decrease in Adhesion Performance of Waterproofing Layers on Slabs with Pavements Cuts
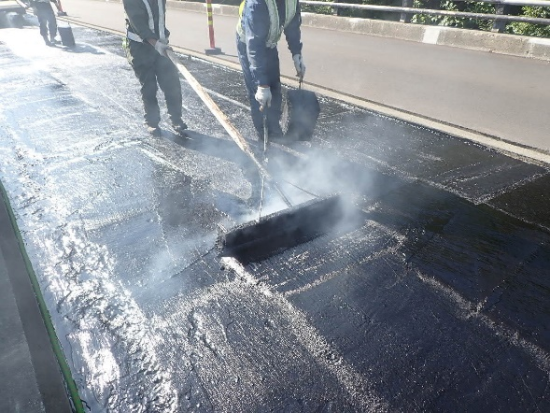
Figure-1 The installation of the HRA
waterproofing layer
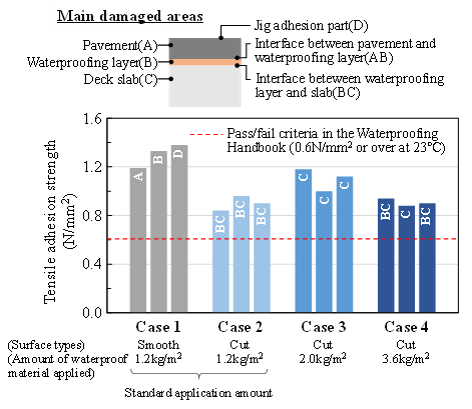
Figure-2 Results of
the tensile adhesion test
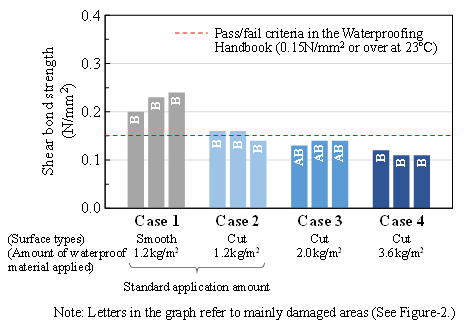
Figure-3 Shear test results
To ensure the long-term durability of concrete slabs on highway bridges (hereinafter referred to as “slabs”), it is necessary to prevent the intrusion of rainwater and other elements from the road surface. For this reason, slabs where deterioration or damage has become apparent or where a waterproofing layer has not yet been installed have a waterproofing layer installed during bridge repair to contain deterioration and/or damage and to achieve preventive maintenance (Figure-1).
The installation of a waterproofing layer during bridge repairs tends to follow these steps: (1) the removal of the existing pavement with a cutting machine, (2) the installation of the waterproofing layer, and (3) the restoration of the pavement.
However, it has been pointed out that a waterproofing layer installed on a slab surface with pavement cuts (hereinafter, “the cut surface”) has less waterproofing performance (resistance to water intrusion) and less adhesive performance (cohesion with the slab and pavement) than a waterproofing layer installed on a slab surface without cuts.
Therefore, the Structures Research Team is conducting research on techniques to improve the performance of waterproofing layers when these are installed on existing slabs. In this issue, we present a case study of the decrease in adhesive performance in a waterproofing layer installed on a cut surface.
We conducted laboratory tests on hot-rubberized asphalt (HRA) waterproofing to examine how the type of surface (smooth or cut) on which the waterproofing layer is installed and the amount of HRA waterproofing material applied affect the adhesive performance of the waterproofing layer. The tests were conducted in accordance with the tensile adhesion test and the shear test of the Handbook for Highway Bridge Slab Waterproofing Journal of the Japan Society of Erosion Control Engineering (Japan Road Association, March 2007) (hereinafter referred to as “the Waterproofing Handbook”). The tests found the following.
1) The tensile adhesion strength of the HRA waterproofing layer was lower on a cut surface than on a smooth surface because micro-cracks occurred on the concrete surface from impacts during cutting operations, and these micro-cracks acted as weakening points (Figure-2).
2) For the HRA waterproofing layer installed on the cut surface, we observed that the waterproof material thickness was greater in the grooves of the cut surface, resulting in a decrease in shear bond strength, and that the decrease in bond strength became more pronounced with increase in the amount of waterproof material applied (Figure-3). We also found that, when a waterproofing layer is installed, the application of more waterproof material than the standard amount may result in an adhesive strength that fails to meet the pass/fail criteria in the Waterproofing Handbook.
In bridge repair, it is assumed that one property of the cut surface―the degree of unevenness―will vary from site to site; however, the relationship between this property and adhesion performance has not been assessed in previous studies. In the future, we plan to ascertain this property through field surveys and to conduct additional tests based on the results of the field surveys, in order to study quality control methods for the installation of a waterproofing layer (control items, methods for performance verification).
(Contact: Structures Research Team, CERI)
Effort to Promote a Concrete Pavement Repair Method That Utilizes an Insulating Material
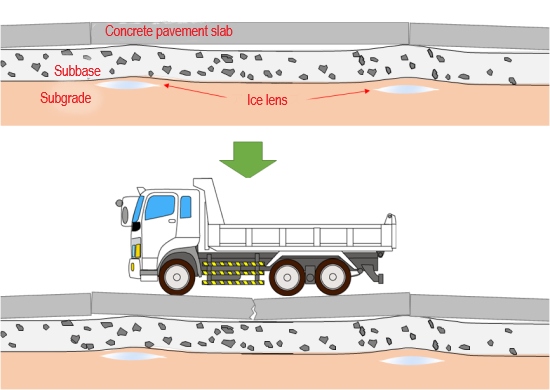
Figure-1 Example of concrete pavement
damage due to frost heaving
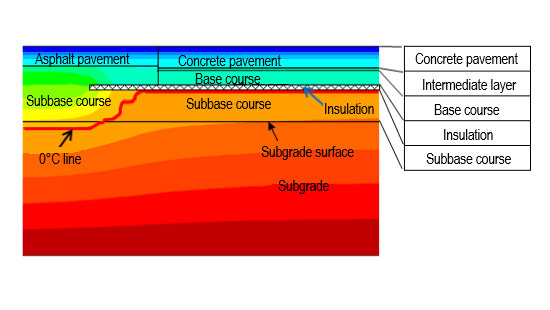
Figure-2 Example of heat transfer
analysis results
1. Introduction
Concrete pavements are more durable against rutting and cracking than asphalt pavements, and they are expected to reduce life cycle costs by extending the pavement lifespan. However, a concrete pavement has a slab structure that resembles a plate (Figure-1), and if it cannot conform to the growing unevenness caused by frost heaving, as shown in the figure, then it will crack early from traffic loads. For this reason, concrete pavements in snowy, cold regions require more extensive measures against frost heaving than asphalt pavements require.
Meeting that requirement may entail additional measures against frost heaving when attempts are made to replace aging asphalt pavement with more durable concrete pavement. Conventional construction methods in such cases require digging to the frost-penetration depth and replacing the soil that would freeze with materials that do not arize frost heaving, which increases construction costs and time. To solve this problem, our team has been researching the application of insulating materials that suppress frost penetration (an insulation method), and this issue introduces these efforts.
2. Evaluation by test installation, and the dissemination of the method
The insulation installation depth was determined based on heat transfer analyses (Figure-2), and test installation (Photo-1) was conducted to examine the heat insulation effect. It was found that insulating materials enable a reduction in the depth to which measures against frost heaving are applied compared to conventional methods, while at the same time achieving sufficient frost heaving prevention.
We have prepared the Design and Construction Manual for Concrete Pavement Repair Using Thermal Insulation (Draft) (Figure-3), which summarizes a series of points to be considered from design to construction so that the manual can be used in pavement repair work. This achievement is also reflected in the Road Design Guidelines of the Hokkaido Regional Development Bureau of the Ministry of Land, Infrastructure, Transport and Tourism. The technology is expected to reduce the construction costs and time associated with measures against frost heaving compared to conventional methods and is expected to contribute to the promotion of concrete pavements by providing life cycle cost advantages over asphalt pavements.
![]() (The insulation prevents frost penetration.) |
![]() Repair Using Thermal Insulation (Draft) |
(Contact : Road Maintenance Research Team, CERI)