A Draft Guideline for the Effective Use of Recycled Concrete Coarse Aggregate in Precast Concrete
Recycled Aggregates for Concrete: The Current Situation
Each year. Approximately 30 million tons of concrete structures are demolished. Innovative Materials and Resource Research Center (iMaRRC) is conducting research on how to reuse this demolished concrete as material for new concrete.
Concrete is made from gravel (coarse aggregate), sand (fine aggregate), water, and cement. The volume ratio of these materials is roughly 4:3:2:1(Photo 1). The idea of reusing demolished concrete as a substitute for gravel has existed for years. It is called recycled concrete aggregate. Japan Industrial Standards (JIS) are established for the quality of recycled concrete aggregate. There are three classes―H, M, and L―arranged in order from the highest quality (Photo 2). Class H consists almost entirely of natural aggregate extracted from demolished concrete and therefore has good quality. However, it takes a considerable amount of cost in order to remove original cement paste from the demolished concrete. In addition, gravel accounts for only about 40% of the material contained in the concrete. The other components become fine powder whose disposal can be problematic. Class L can be produced by crushing demolished concrete to an appropriate particle size. However, it cannot be used in structural concrete due to its inferior quality. Class M can be used in structures, but it is limited to areas that are less affected by weather (e.g., areas underground), and therefore its use is not widespread.
Outline of a Draft Guideline
In light of this situation, we prepared a draft guideline for the effective use of Calss M recycled aggregate in precast concrete (Figure 1). “Precast concrete” is a concrete product manufactured in a factory. This characteristic makes quality control easier and can diminish cracking risk by limiting product size even when using recycled aggregate concrete, which is prone to shrinkage due to drying. Additionally, we have confirmed in laboratory tests and outdoor exposure tests that precast concrete made with recycled aggregate possesses conditions that can ensure frost damage resistance equivalent to that of ordinary concrete even in cold regions where deicing salts are splayed(Figure 2, Photo 2)..
The draft guideline can be downloaded from https://www.pwri.go.jp/team/imarrc/research/tech-info.htmlWe hope it will provide useful in promoting the use of recycled concrete aggregate.
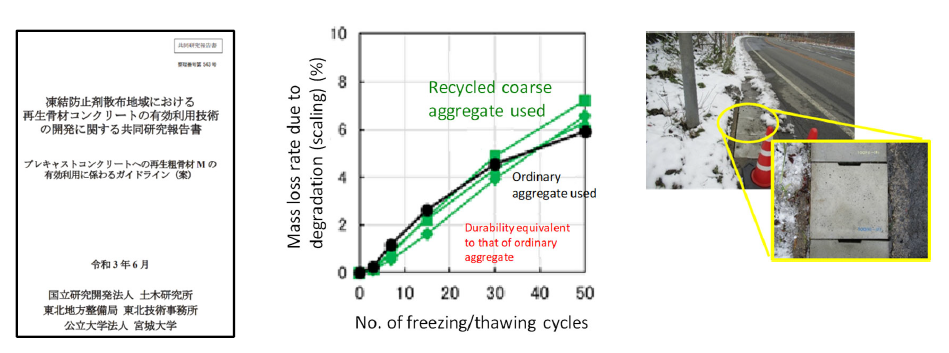
(Contact: Innovative Materials and Resources Research Center)
3D Flood Hazard Map That Is Easy to Understand and Use
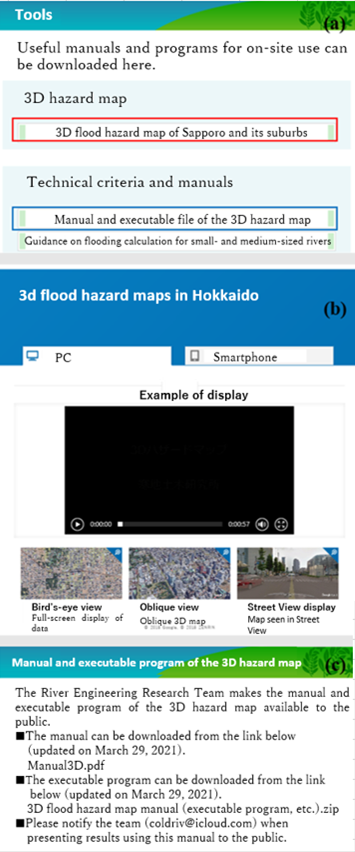
(a) screenshot of the tools on the River
Engineering Research Team’s website,
(b) examples of maps created,
(c) software and manual
1. Background and purpose
In recent years, floods of an unexpected and previously unexperienced scale have increased, resulting in an increase in the number of residents who receive evacuation orders. However, flood hazard maps that provide useful information to residents during evacuation are not well-recognized. Therefore, the River Engineering Research Team has developed a “hazard map that is easy to understand and use” using Google Earth to enable residents to detect risks and evacuate voluntarily.
2. Characteristics of the 3D flood hazard maps
Conventional hazard maps have two problems: (1) Travelers who are not familiar with the area cannot find the flood depth of their location as they do not know where they are on the hazard map and (2) the flood depths look unrealistic because they are only distinguished by different colors.
Therefore, the River Engineering Research Team developed technology to draw flood depths on Google Earth and Street View. By seeing this map, people can know their location by using the GPS function of their smartphones, and see the expected flood conditions at all heights and angles. Figure 1 shows an example of the map display. Another major characteristic of the map is that the 3D models of land features, buildings and streets already created by Google can be used as they are.
3. For dissemination of the technology
To disseminate the 3D flood hazard map, a software and a manual describing how to use it were made available on the team’s website. By using these, a 3D flood hazard map can be created at no cost. The screen shown on Fig. 2 (a) will appear by accessing https://river.ceri.go.jp/contents/tool/. Then, by clicking on the red frame, the screen with explanations on how to download a created 3D flood hazard map and other information will appear as shown in Fig. 2 (b). By clicking on the blue frame in Fig.2 (a), the software and manual on how to create a map can be downloaded as shown in Fig. 2 (c).
Advantages of this technology are: (1) flood conditions can be grasped in an intuitive manner, (2) maps can be made at low cost, (3) maps can be made in multiple languages, (4) maps can be used for disaster reduction education, and (5) maps can be easily changed when shelter information is revised.
(Contact: River Engineering Research Team, CERI)